Diamond blades are, renowned for their durability and precision, however, even the highest-quality blades can succumb to damage if not used correctly. Understanding common issues that affect diamond blades maximises their lifespan and cutting performance. In this blog post, we'll delve into common faults encountered with diamond blades, shed light on potential user errors, and provide actionable tips to prevent damage and prolong blade lifespan.
Common Diamond Blade Faults:
- Uneven wear patterns indicate improper blade alignment or usage, resulting in reduced cutting performance and blade longevity
- Blade warping occurs when subjected to excessive stress or force, leading to a distorted shape and compromised cutting accuracy
- Clogging: Accumulation of debris and material on the blade surface can hinder cutting efficiency and increase the risk of blade overheating
Understanding Common User Errors:
- Incorrect Blade Selection: Choosing the wrong blade for the material being cut can fast-track wear and lead to blade failure. This can include core cracks.
- Improper Operation: Operating the diamond blade at incorrect speeds or applying excessive pressure can cause overheating and premature wear.
- Lack of Maintenance: Neglecting routine maintenance, such as cleaning the blade and checking for damage, accelerates wear and increases the likelihood of faults.
- Ignoring Safety Guidelines: Failing to adhere to safety protocols not only endangers personnel but also increases the risk of blade damage due to mishaps.
The Specifics:
Loss of Tension:
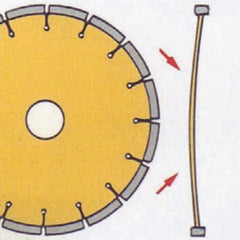
Excessive heat build-up, particularly when cutting in wet conditions, highlights the need for an ample water supply. Verifying the machine's Rotations Per Minute, flange sizes, and bearing condition is crucial to maintain proper operation. If the blade is excessively hard for the intended application, it may deviate during cutting. Securing the blade on the spindle and preventing spinning is essential. Ensure the blade is used to cut in straight lines only, maintaining blade stability and preventing tension loss.
Undercutting:
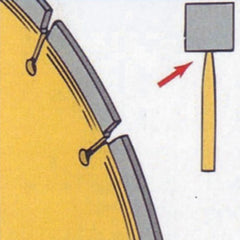
Undercutting is a significant concern, especially in abrasive materials like asphalt and fresh concrete, leading to premature wear of the steel core and potential segment loss. This occurs when the steel core wears to a sharp edge just beneath the segment. Ensuring the blade specification includes offset segments that can aid in slurry removal during cutting. Moreover, it's crucial to avoid cutting below the asphalt into the sub-base, as continual contact with loose material fast-tracks wear without improving the cutting surface. Proper water supply is also essential, as adequate flow can wash slurry away, reducing undercutting.
Uneven Segment Wear:
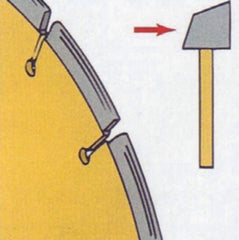
If you notice uneven segment wear on your blade, it could be due to worn-out bearings, damaged bearings, or a worn bore hole. In such cases, it's crucial to replace or repair the bearings or shaft as needed to restore proper functionality. Uneven wear patterns can result from insufficient water during wet cutting. Excessive cutting pressure, often caused by too high infeed, can cause the blade core to bend and flex. Additionally, it's important to check the alignment of the blade, including the wheels and wheel alignment for floor saws, and the carriage alignment for masonry bench saws.
Rapid Wear:
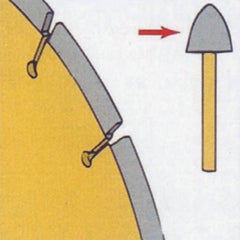
Use the correct blade specification for the material being cut to avoid over-exposing the diamond blade. Check the bearings and the spindle, if they’re worn then replace them before fitting a new blade. If the output power is insufficient try replacing worn belts, checking the voltage and using an electric extension of the proper size. Ensure adequate water supply to reduce wear and clean the cooling system.
Core Cracks:
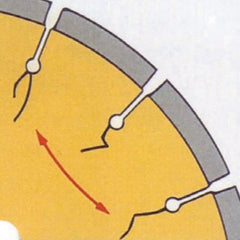
When the blade is too hard for the material being cut, it can cause core cracks. Excessive cutting pressure or blade jammed or twisted can lead to the blade core bending and flexing, eventually resulting in metal fatigue and core cracking. Moreover, worn shafts, damaged machine bearings, or incorrectly mounted blades can also contribute to this issue. Use sufficient water to cool blades for wet cutting, while for dry cutting, allow air to circulate around the blade to prevent overheating.
Segment Loss:
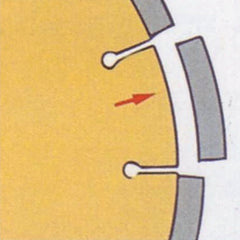
Segment loss could occur if the blade twists or jams in the cut due to failure to hold the material firmly, or if the machine has been twisted or turned while cutting. Using a blade that's too hard for the material being cut, causes excessive polishing, and breaking off the segment. Avoid cutting below the asphalt into the sub-base to prevent blade core undercutting. Check for foreign materials between the blade core and flange, which can cause excessive impact or fatigue and replace the flanges if necessary.
Segment Cracks:
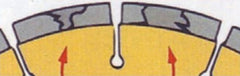
Cracked segments are from the blade being too hard for the material, the blade specification should match the material being cut. Use the correct blade type and consider a softer bond system if necessary. Excessive cutting speed can also be a factor, try reducing the speed of advance.
Eccentricity:
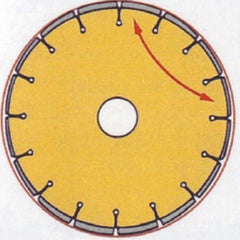
If the blade is too hard for the material being cut, it may hammer and wear out of round. In this situation, selecting a blade with a softer bond system is recommended. A machine spindle may have a groove scored in it from a previous blade slipping, replace the spindle if it’s worn or is no longer properly aligned. A blade being out of round could be due to worn blade shaft bearings, replacing the bearings and ensuring regular lubrication is essential.
Overheating:

Excessive heat build-up is a leading cause of diamond blade damage. It occurs due to prolonged use without proper cooling or operating at incorrect speeds. Overheating usually causes discolouration of the core, either black or blueish. To mitigate this, ensure adequate water supply for wet cutting blades and inspect water tubes for blockages or damage. Additionally, avoid excessive cutting pressure for dry cutting blades; only use dry disks for shallow cuts and let the blade turn freely every 10-15 seconds to allow air to cool it.
Damaged or Distorted Bore Hole:
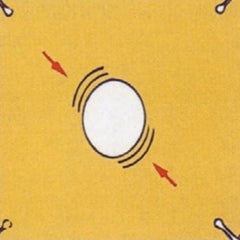
If the blade is incorrectly aligned during mounting, it may hammer. Check the blade is placed on the correct diameter spindle before tightening and that the pin holes align with the drive pin. Improper tightening of the flanges can cause the blade to spin or vibrate on the spindle, make sure to tighten the nut on the spindle with a spanner. If the saw shaft is badly worn or grooved, the blade may pound during operation.
Blade Not Cutting:
Select the appropriate blade specification for the material to be cut, see the blade application chart or consult your distributor/manufacturer who will indicate the proper blade for the material. Consider re-sharpening dull blades using soft abrasive materials, however if the blade becomes too dull then it is too hard for the material. Verify correct rotation direction and machine horsepower for blade specifications, check the belts, the voltage and the motor output power.
Tips to Preserve Diamond Blade Integrity:
- Choose the Right Blade: Select a diamond blade specifically designed for the material and application to ensure optimal performance and longevity.
- Follow Manufacturer Guidelines: Adhere to recommended operating speeds, pressure levels, and cooling methods as specified by the blade manufacturer.
- Practice Regular Maintenance: Clean the blade after each use to remove debris and inspect for any signs of damage or wear. Replace worn or damaged blades promptly.
- Use Cooling Methods: Employ water or cooling agents to dissipate heat and minimise the risk of overheating during cutting operations.
- Prioritise Safety: Educate personnel on proper handling techniques and safety precautions to prevent accidents and protect individuals and equipment.
- The tool is warped: withdraw any warped tool, if it is almost new then it may be straightened by the supplier.
Conclusion:
The integrity of diamond blades is crucial for achieving smooth and efficient cutting operations. By understanding diamond blade faults and addressing potential user errors, construction professionals can enhance blade performance, minimise downtime, and extend blade lifespan. Every proactive measure taken to preserve diamond blade integrity contributes to enhanced productivity, cost savings, and overall project success.
By implementing proactive maintenance practices and adhering to manufacturer guidelines, users can maximise the value of their diamond blade investments while achieving superior cutting results.
Check out our collection of Diamond Blades by clicking here!
With thanks to:
https://www.nortonabrasives.com/en-us/resources/expertise/diamond-blade-troubleshootinghttps://www.udt.com.au/view/diamond-blades/diamond-blade-tips-and-troubleshooting